Seasteading tech for ten thousand startup countries our best chance for liberty
The Seasteads are Here
Learn about the revolutionary technology for eco-restorative ocean communities and our plan to secure political autonomy for all seasteaders.
The Seasteading Institute is a nonprofit organization.
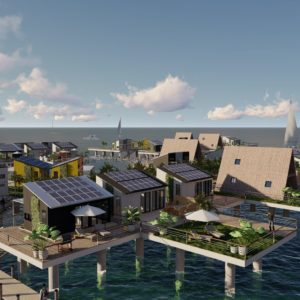
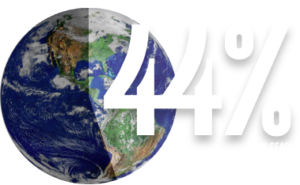